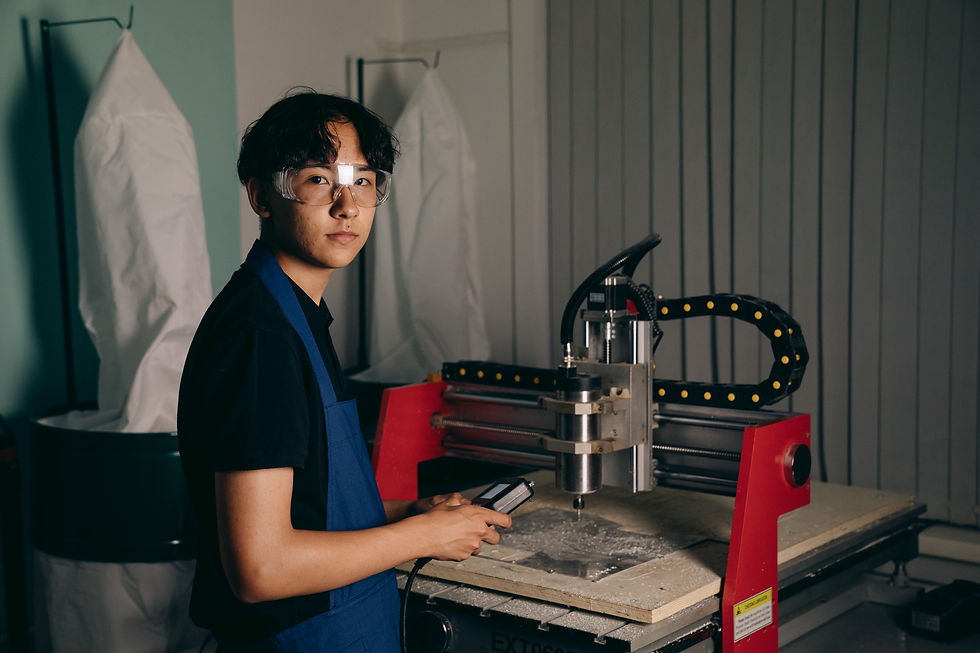
CNC machine tool spindle crashes can be costly and disruptive, but with the right precautions, they can be minimized. Here are some key causes of spindle crashes and best practices to avoid them, particularly focusing on RPM spindles.
Common Causes of Spindle Crashes:
Programming errors: Inputting incorrect coordinates, tool paths, or feed rates can lead to unexpected movements and collisions with the workpiece or fixtures, including RPM spindles.
Tooling issues: Using improper tooling, such as oversized or excessively long tools, can result in collisions between the RPM spindle and the workpiece.
Workpiece-related problems: Poor workpiece positioning or inadequate work holding can cause the RPM spindle to collide with the material.
Machine setup errors: Misaligned fixtures, inaccurately positioned workpieces, or improper tool setup can lead to RPM spindle crashes.
Sensor or feedback system failure: Faulty sensors or feedback systems may not accurately detect the position of the RPM spindle, increasing the risk of collisions.
Preventive Measures for RPM Spindle Crashes:
Verify CNC programs: Double-check and simulate CNC programs to ensure accurate coordinates, tool paths, and feed rates. This helps identify potential collision risks before running the program on the machine with the RPM spindle.
Conduct test runs: Prior to critical operations, perform test runs at reduced speeds to validate the program and identify any collision risks involving the RPM spindle.
Implement tool length and diameter checks: Use compensation features to account for tool length and diameter, preventing collisions caused by incorrect tool sizes. Regularly update tool data to maintain accuracy.
Ensure proper workpiece setup: Securely and accurately clamp or fixture the workpiece to avoid interference with the RPM spindle and tooling. Check for potential collisions before commencing machining.
Regular machine maintenance: Inspect and maintain the machine, including RPM spindles, sensors, and feedback systems. Promptly replace worn-out or damaged components to prevent unexpected failures.
Provide operator training: Train CNC machine operators thoroughly on programming, setup, and safe operating practices, emphasizing error checking and vigilance to reduce the risk of RPM spindle crashes.
Implement safety measures: Install protective guards and barriers around the machine to prevent accidental contact with the RPM spindle. Utilize sensors and limit switches to detect abnormal movements and automatically stop the machine if necessary.
By adopting these preventive measures and prioritizing safety and attention to detail, the risk of RPM spindle crashes can be significantly reduced. This ensures smoother and more efficient machining operations, minimizing downtime and costs associated with spindle crashes.
Commentaires